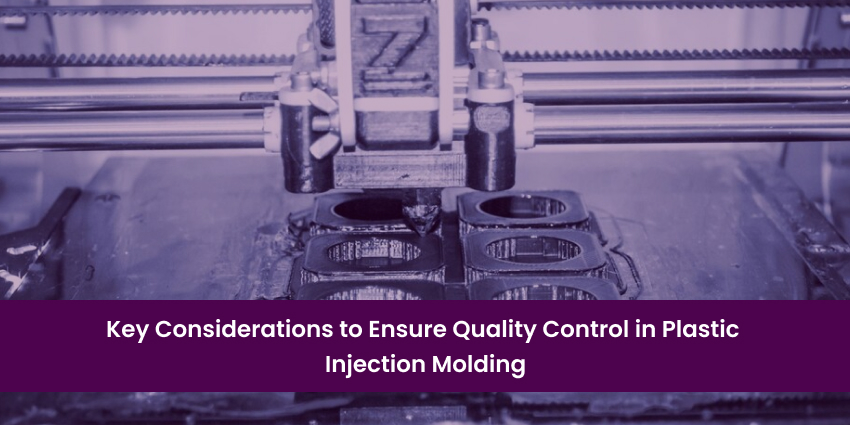
What’s the secret to producing flawless plastic parts, time after time? How can manufacturers minimize costly defects and maximize efficiency in injection molding? The answer lies in a comprehensive approach to quality control.
This blog post breaks down the essential elements of achieving superior quality in plastic injection molding, from material selection and design to process optimization, advanced inspection techniques, and the latest technological innovations.
Join us as we explore the key strategies for ensuring consistent, high-quality results in this vital manufacturing process.
Key Elements of Quality Control in Injection Molding
To ensure top-notch quality in plastic injection molding, several key elements must be carefully considered and managed. By focusing on these elements, manufacturers can minimize defects, reduce costs, and maximize efficiency.Material Selection
-
Thermoplastics vs. Thermosetting Plastics:
-
Material Properties:
-
Material Consistency and Purity:
-
Sustainable/Recycled Materials:
Design for Manufacturability (DFM)
Optimizing Part Geometry: A simple, functional design is key to efficient injection molding. Optimizing part geometry ensures smooth mold filling, uniform cooling, and easy ejection. By applying DFM development services, manufacturers can reduce defects, lower production costs, and improve part quality. Uniform Wall Thickness: Maintaining uniform wall thickness is essential to prevent issues like warping and sink marks. It also reduces material waste, ensuring better part quality and more predictable results. Draft Angles: Draft angles (1-3 degrees) on vertical surfaces ease part ejection from the mold, reducing friction during ejection and improving part quality. Ribs, Bosses, and Undercuts: Ribs add stiffness without excessive weight, while bosses are essential for fastening. Minimizing undercuts reduces mold complexity and costs. Efficient design ensures better injection mold design services. Simulation Tools (FEA and CFD): Finite Element Analysis (FEA) helps optimize strength and durability, while Computational Fluid Dynamics (CFD) simulates molten plastic flow, ensuring uniform filling, optimal cooling, and minimized defects. By applying DFM principles, manufacturers can reduce defects, lower production costs, and improve product quality.Mold Design and Maintenance
Precision in Mold Manufacturing: Accurate molds with tight tolerances and precise machining ensure proper part dimensions, reducing defects and enhancing overall quality. A skilled tooling company ensures top-tier precision for both plastic injection molding tooling and metal additive manufacturing services. Regular Mold Maintenance: Routine cleaning, lubrication, and inspection extend mold life and reduce downtime. Maintaining molds with precise tooling solutions ensures continued production efficiency. Mold Wear and Tear: Over time, molds can suffer from wear caused by abrasion, corrosion, or impact. Regular inspections help identify early signs of wear, allowing for timely repairs before they affect part quality. Preventive maintenance can significantly reduce the risk of costly downtime. Mold Cooling Channels: Efficient cooling is crucial for reducing cycle time and preventing issues like warping or uneven cooling. Properly designed cooling channels help achieve uniform temperature distribution, ensuring that the part cools evenly and maintains consistent dimensions throughout the molding process.Injection Molding Process Optimization
Injection Pressure, Speed, and Cooling Time: These parameters are critical for achieving high-quality parts. Proper settings ensure the mold is completely filled, minimize defects, and optimize the cycle time for efficiency. Balancing these factors helps in achieving consistent results and reducing the occurrence of issues like incomplete filling or excess material. Melt Temperature: Maintaining the correct melt temperature is key for ensuring uniform material flow and preventing material degradation. Overheating can lead to material breakdown, while too low a temperature can result in poor flow and weak parts. Consistent temperature control ensures a smooth and efficient molding process. Gate and Runner System Design: The gate is where molten plastic enters the mold cavity, and the runner system channels the material to each gate. A well-designed gate and runner system ensures even material distribution, minimizing defects like air pockets, flow marks, or uneven fill. Optimizing this system is essential for consistent part quality. Minimizing Cycle Time: Optimizing process parameters such as injection speed and cooling time helps reduce cycle time. However, this should never compromise part quality. Fine-tuning these parameters ensures faster production without sacrificing the integrity of the molded parts.Quality Assurance Techniques
Statistical Process Control (SPC): SPC uses statistical analysis to monitor and control the injection molding process, identifying trends and deviations from target values. By analyzing process data in real time, it helps detect potential issues early, ensuring consistent quality throughout production. Automated Inspection Systems: Technologies like vision systems, laser scanners, and coordinate measuring machines (CMMs) provide rapid and accurate dimensional measurements. These systems can inspect parts automatically, reducing human error and increasing the consistency and efficiency of the inspection process. Non-Destructive Testing (NDT): Techniques such as ultrasonic testing and X-ray inspection allow for the detection of internal defects without damaging the part. These methods are essential for ensuring the structural integrity of parts, particularly in high-stress applications where internal flaws could lead to failure. Inspection Checkpoints: Implementing inspections at various stages of the production process ensures defects are detected early. Regular inspections during molding, post-molding, and final quality checks help in identifying and resolving issues before they affect the final product, ensuring high-quality standards.Common Defects and Their Solutions
Warping: Warping occurs when uneven cooling or residual stresses distort the part shape. Solutions include optimizing cooling rates, using ribs to strengthen the part, and adjusting process parameters such as injection pressure and cooling time to ensure uniform stress distribution. Sink Marks: Sink marks are depressions that form on the surface of thick sections as they cool and shrink. To prevent this, reduce wall thickness, add ribs to support the part structure, and optimize cooling to ensure even heat dissipation. Voids: Voids are internal air pockets that can result from insufficient material flow or improper venting. Solutions include increasing injection pressure to fill the mold cavity fully, optimizing venting to allow air to escape, and adjusting the melt temperature to improve flow consistency. Flash: Flash occurs when excess material leaks out between mold halves due to improper clamping. Solutions involve adjusting the injection pressure to prevent overflow, improving the mold fit for tighter tolerances, and ensuring the clamping force is properly calibrated to prevent gaps. Burn Marks: Burn marks are discolorations caused by trapped air or excessive heat, often seen as dark spots on the part. Solutions include improving venting to allow trapped air to escape, reducing injection speed to minimize heat buildup, and adjusting the melt temperature to avoid overheating the material.Training and Workforce Development
- Skilled Operators: Trained operators are essential for setting up, monitoring, and troubleshooting the injection molding process.
- Regular Training: Ongoing training on new equipment, processes, and quality control techniques is crucial.
- Culture of Quality: Fostering a quality-conscious environment among all team members is essential for maintaining high standards.
Technology Integration
IoT and Sensors: IoT sensors play a crucial role in real-time monitoring of process parameters, collecting valuable data that enables precise process control and continuous optimization. These sensors help manufacturers detect anomalies early, ensuring better consistency and fewer defects in production. Digital Twin Technology: Digital twin technology creates a virtual replica of the molding process, allowing for real-time testing and simulation. This virtual model helps identify potential issues before physical production begins, optimizing efficiency and reducing costly errors in the actual manufacturing process. AI and Machine Learning: AI and machine learning analyze vast amounts of data collected from production processes. These technologies predict potential defects, optimize key parameters like injection pressure and cycle time, and even automate quality control tasks, improving overall product quality and reducing the need for manual intervention.Documentation and Traceability
Production Logs: Maintaining detailed production logs, including records of process parameters, material batches, and inspection results, is essential for troubleshooting and continuous improvement. These logs provide valuable insights that help manufacturers identify trends, diagnose problems, and make data-driven decisions. Traceability Systems: Advanced traceability systems track parts throughout the production process, allowing manufacturers to trace a part’s history back to specific batches and parameters. This enables quick identification and resolution of defects, improving the overall reliability and consistency of products. Compliance: Adherence to industry standards such as ISO 9001 is essential for ensuring quality control and meeting customer requirements. Compliance guarantees that processes meet rigorous quality criteria, enhancing the trust and reliability of the manufacturer in the eyes of the customer.Sustainability in Quality Control
Reducing Material Waste: By optimizing the injection molding process and minimizing defects, manufacturers can significantly reduce material waste. Efficient material use not only lowers production costs but also minimizes the environmental impact of the manufacturing process. Recycle and reuse materials when possible to ensure a more sustainable operation. Recycled Materials: Using recycled materials in injection molding is an effective way to reduce environmental impact. However, the properties of recycled materials can vary, so it’s important to test and adjust process parameters to ensure consistent quality. In some cases, blending recycled material with virgin material can help achieve the desired balance of performance and cost. Design for Recyclability: As part of a broader sustainability strategy, designing parts for recyclability is essential. This includes designing for easy disassembly, using materials that are easier to recycle, and minimizing the use of mixed materials that are difficult to separate. Recyclable designs contribute to the circular economy and help reduce the environmental impact of manufacturing.Conclusion
Ensuring quality control in plastic injection molding is not just about avoiding defects—it’s about building a robust process that consistently delivers high-quality results. By focusing on key elements like material selection, design for manufacturability, mold design, process optimization, and leveraging advanced technologies, manufacturers can achieve greater efficiency, reduce costs, and enhance product reliability. As the industry evolves, integrating tools like IoT, AI, and digital twins will further refine quality assurance practices, making them smarter and more predictive. At the same time, prioritizing sustainability through the use of recycled materials and waste reduction aligns manufacturing goals with environmental responsibility. With a comprehensive and proactive approach to quality control, manufacturers can not only meet customer expectations but also maintain a competitive edge in today’s demanding markets. Looking to optimize your injection molding services? Our team of experts specializes in delivering tailored solutions to optimize quality and efficiency at every stage. Contact us today to learn how we can help you achieve superior results in plastic injection molding.FAQs
What is the difference between gate and runner systems in injection molding?
The gate is the entry point for the molten plastic to enter the mold cavity, while the runner system is the network of channels that distributes the material from the injection molding machine to the gates. Proper design ensures uniform material flow and reduces defects.How do I determine the optimal injection molding process parameters for a specific material?
Determining optimal parameters requires understanding the material’s properties (e.g., melt temperature, viscosity, cooling rate) and running tests to fine-tune settings like injection pressure, speed, and cooling time for consistent results.What steps can I take if my recycled material causes defects in the final product?
If recycled materials lead to defects, consider blending them with virgin materials, testing the material’s properties for compatibility, or adjusting process parameters such as temperature and pressure to accommodate variations.How can I identify and address potential wear and tear in molds before it causes quality issues?
Regularly inspect molds for signs of wear, such as surface roughness, dimensional changes, or corrosion. Implement preventive maintenance schedules, including cleaning, lubrication, and polishing, to extend mold life.Visited 8 times, 1 visit(s) today